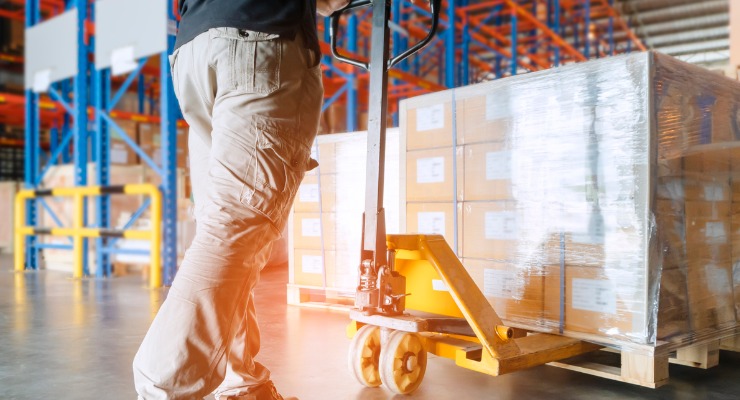
For many businesses, their supply chain management (SCM) can make or break them. Letting down customers and losing sales is the last thing any business needs in this tough economic climate. The problem is business owners often feel they have little control over their supply chain. However, there are actions they can take to mitigate some of the risks and disruptions associated with supply chains. Here’s what you can do.
Understanding Business Risks
Business risks can be classified as either internal or external. An internal risk is one you have control over, whereas external risks are those you have no control over. Unfortunately, supply chains fall under external risk as they are something that cannot be controlled. Risks associated with supply chains are generally those that can cause a disruption to the availability of raw materials, parts or the finished product. This makes it extremely important for businesses to have SCM strategies in place.
The coronavirus has made many business owners rethink their approach to supply chains, realising that they need to be planning for worst case scenarios and to be ready for anything.
Identifying Risks as Part of Your SCM Strategy
When it comes to risk management within a business, owners/managers must be able to identify any and all relevant risks. It’s a case of thinking about every scenario that may occur, before considering the ramifications these particular scenarios could have on your business. Risk management plays a key role in SCM strategies, as it can be put into place to help businesses analyse, evaluate, treat, monitor and even completely avoid problems that arise from risks. It is extremely important to understand how your business could be affected by problems that arise from risks. With this in mind, it may be worth asking yourself a range of questions, including:
-
What, when, where, how are risks likely to occur in the business?
-
Are the risks internal or external?
-
Who may be affected by the worst case scenario?
Consider the consequences of events like:
-
Natural disasters/Acts of God.
-
Loss of electricity supply.
-
No internet access.
-
Suppliers going out of business.
-
Loss of key personnel.
-
Important documents being lost or stolen.
-
Customer data being lost or stolen.
Management of Risk and Disruption in the Supply Chain
If you’ve identified the loss or disruption to your supply chain as a possible risk, it may be due to your:
-
Your supplier closing its business.
-
Your supplier's factory becoming damaged or being destroyed.
-
Your supplier's staff being unavailable due to illness, injury or industrial action.
-
Raw materials or parts being unavailable.
-
Product misplacement or theft.
-
Transportation being unavailable.
-
Terrorism.
-
Overseas government interference.
Keeping Stock on Hand
Some businesses are luckier than others in terms of access to stock within their supply chains. For example, a building company may feel confident that it can purchase enough of a product (cement, bricks, etc.) from multiple sources, rather than just relying on one supplier. This means that there might be no need to keep certain products in stock all the time, as the company can place the order and have it delivered to the site on the same day. This also ensures that there’s no double handling, storing and stock on-hand costs.
However, when a business relies on a product being delivered from overseas, delivery times are much longer and the risks are greater. Keeping plenty of stock on-hand is one way to reduce supply chain risks, but the upfront cost associated with this can place a strain on cash flow. This can result in companies looking for cheaper alternatives, however a good amount of strategic planning could be undertaken to help reduce the risks associated with the management of stock. Not all businesses and situations are the same, so there may be instances, industries or businesses that use mathematics and management science are used to inform decisions and optimise some elements of a supply chain. This is known as supply chain engineering (SCE).
Speak to Your Supplier
It's important that you speak to your supplier or suppliers when auditing supply chains. Let your supplier know you’re doing a review of the risks to your business and ask how they would cope if they were faced with adversities, such as a fire in their factory or loss of electricity supply. It's also important to know if your supplier or suppliers own multiple factories that could shoulder the production load quickly if something were to happen. When suppliers don't have contingency plans for things like this, it can affect their customers greatly. So, if it becomes clear to you that your supplier doesn't have the necessary back-up plans to keep things running in the face of adversity, you may want to consider using another supplier.
Replacement Supplier
Do your research and source a back-up supplier. If your current supplier closed its factory tomorrow, you may need to be able to make contact with an alternative supplier and ask them to start producing immediately. You'll want to ensure the back-up factory isn’t in the same location in case of a natural disaster or government interference. However, different geographic locations of suppliers further increases your risk. There are services available that may be worth taking advantage of, including speaking with an import agent who has a good relationship with reputable factories, as these services can help to keep the supply chain moving at short notice.
Additionally, you might want to discuss the factory’s ability to fulfill the size of your orders. Checking with all your suppliers as to how they access raw materials needed to continue manufacturing if there was a shortage can help to further understand the supply chain and will help you learn what to expect. If possible, place a test order or go through the sampling process to ensure you’re also happy with the quality.
Transport Risk
In some cases, even when the goods are out of the factory on time, they may be late or never even arrive if there are transport problems. Your goods may be bumped from the ship at the last minute by a more profitable container, so it's important to have a good relationship with the shipping line to reduce your risk of being bumped. An agent that ships for multiple companies or clients is considered more valuable than a single business importing goods.
Think about what you would do if your goods were lost at sea in wild weather and ensure you have enough stock to cover you while replacement goods are manufactured. Shipped goods are lost and stolen more often than you might think so it’s important to have a plan for that event.
If 2020 has taught us a lesson, it’s that anything can happen.
If you need to safeguard your business against potential supply chain problems, please contact Vara Allied online.